WORKING SAFELY WITH HYDRAULICS
- Barry Michael Aldridge
- Oct 6, 2022
- 5 min read
Updated: Jun 26, 2023
Loughborough-based Flotec, a trusted and leading supplier of reliable hose and engineering solutions to the rail market, addresses the importance of working safely with hydraulics.
With 26th June 2023 witnessing the launch of Rail Safety Week, an initiative devised by the Rail Forum with full support from Network Rail, everyone and every organisation has a part to play in keeping the UK’s rail network safe.
In this feature and by a way of getting involved with the Rail Safety Initiative, here SME rail supplier Flotec, discusses the importance of hydraulics and the need to be both compliant and safe for the betterment and protection of people.

KEEP COMPLIANT.
It is wise to be savvy to ISO 3457 regulations which specify the requirement of guards and other means to protect personnel from mechanical, fluid, or thermal hazards associated with the operation and routine maintenance of high-pressure machinery.
Working with any high-pressure system carries a risk to limbs, life, equipment, and the environment.

LINE-OF-SIGHT.
Legislation stipulates that any hydraulic machinery where operators are required to work within a one metre line-of-sight of hydraulic hosing, must be protected from potential hose failure.
Important to understand is that both equipment operators and organisations themselves can be held legally accountable if a hose failure occurs.
Costs incurred can include:
• Direct medical expenses
• Injured worker wages during recuperation
• Replacement worker wages
• Loss of production
• Management/supervision time
• Training costs
• Legal expenses
• Court costs and fines
• Insurance premium increase
• Equipment repair and downtime
• Environmental clean-up and fines
UNDERSTANDING THE NEED TO PROTECT PEOPLE.
WHAT CAN THE RAIL SECTOR AND ITS SUPPLY CHAIN LEARN FROM ELSEWHERE?
A high-profile case of a loss of limb to a firefighter due to a hydraulic hose failure, highlights the need to ensure the upmost safety of hydraulic equipment to protect people from injury and harm.
In March of 2014, firefighter Ian McDonald was taking part in a training exercise with his employer, the Scottish Fire and Rescue Service when the cutting gear being used suffered a hydraulic hose failure.
The failure resulted in a jet of high-pressure hydraulic fluid tearing through his heavy-duty PPE glove.
When Ian began to feel a burning sensation and noticed his hand swelling, colleagues took him to hospital.
After an X-ray, it was discovered that Mr McDonald had oil in his hand where the toxic fluid was destroying tissue.
Over a four-year period, Ian suffered a great amount of pain and increasing immobility and underwent 40 operations as doctors did all they could to keep the hand working.
Ian’s hand was finally amputated in June 2018.
LESSONS LEARNED.
An investigation carried out by solicitors revealed an inadequate inspection system and lack of equipment maintenance.
It was also discovered that the hydraulic hose pipe connecting the generator to the cutting gear had tiny punctures to it which had occurred over time after being dragged over broken glass and debris at various incidents.
Worse still, whilst protective hydraulic hose sleeves were available, these had not been fixed to the hosing.
Upon court proceedings, Ian McDonald was awarded £1.5m in damages for his injury.
The case of Ian McDonald highlights the need to regularly inspect and maintain equipment’s hydraulic hosing as well as protect hoses from damage, abrasion and general wear and tear.
After the incident and subsequent legal proceedings, Scottish Fire and Rescue issued the following statement:
"Following a robust investigation into Mr McDonald's injury, we undertook a review of equipment and related safety checks and have taken appropriate steps to minimise the risk of similar incidents happening in the future."
Unfortunately, these steps came far too late for Ian, who now has a prosthetic hand.
This story is a harrowing and stark warning of the need to protect people from hydraulic hose failures.
In this case, fitting a Gates LifeGuard hydraulic hose sleeve would have been instrumental in preventing injury to the victim.

THE DEVASTATING POWER AND FORCE OF A HYDRAULIC HOSE PINHOLE LEAK.
The incident with Ian McDonald demonstrates how when hydraulic fluid is expelled from a tiny hole in the hose, it has the force equivalent to that of a bullet being fired from a gun.
The McDonald story is a frightening example of how expelled hydraulic fluid can penetrate PPE with alarming speed and ferocity.
HOW THE GATES LIFEGUARD SLEEVE WORKS.
The LifeGuard sleeve is slipped onto the hose and clamped at each end.
If a hose burst or pinhole leak occurs, the LifeGuard clamping system allows the hydraulic fluid to safely escape down the length of the hose assembly in a controlled manner.
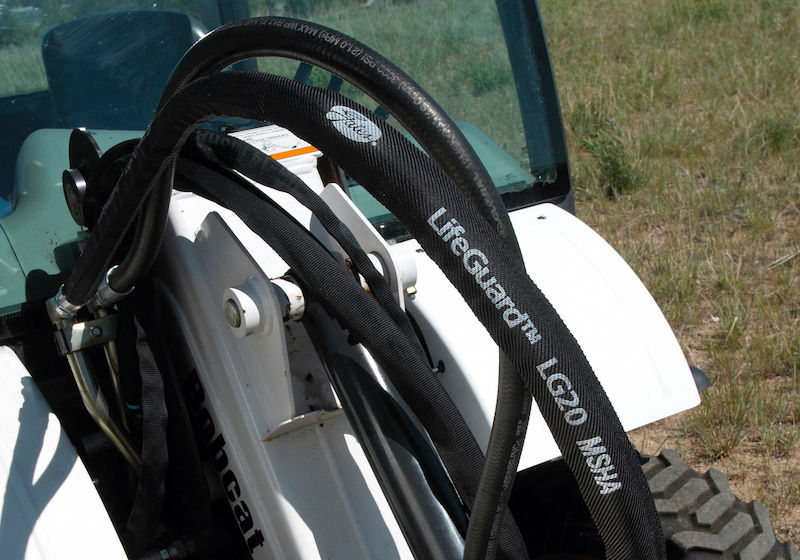
REDUCING FIRE HAZARDS.
Although rare, hydraulic hose failure can also cause hazardous fires and highly combustible situations.
Fires caused by hydraulic hose failure usually occur when a blown hose or pinhole leak expels hydraulic fluid close to high-temperature surfaces such as engines or power generators.
The result can be catastrophic.
Oil Mist is often a major contributor to fires or explosions.
This can occur when high pressure hydraulic fluid is either sprayed through a crack in the hose or fluid leakage from a full hose failure and the hydraulic oil lands on a hot surface, vaporizes and then contacts with a lower temperature.
When the concentration of oil mist increases and reaches the lower explosion limit, a flammable instance may happen when the mist either contacts surfaces over 200°C or interacts with a spark.
SAFETY, QUALITY AND RELIABILITY FROM A TRUSTED SUPPLIER.
As an official Gates Hydraulics distributor, Flotec recommends the LifeGuard hydraulic hose sleeve which has been proven to be successful in containing and safely controlling hydraulic hose bursts and pinhole leaks.
The LifeGuard sleeve has been rigorously tested in both lab and field environments.
The LifeGuard hydraulic hose sleeve is effective in containing pin burst leaks of up to 35,0 MPa and hydraulic hose bursts up to 70 MPa and is capable of fluid containment up to 10,000 psi.
Importantly, the LifeGuard sleeve is fully compliant with ISO 3457 specifications and meets MSHA flame resistance standards.
During 5,000 psi (34.5 MPa) pinhole leak tests, LifeGuard sleeve controlled and redirected fluid while un-sleeved hoses allowed high-pressure spraying of fluids.
The high strength nylon layers and Kevlar material of the LifeGuard sleeves are effective in resisting PPE penetration.
Companies need peace of mind that hydraulic equipment is as safe as can be and that any risk has been mitigated as far as possible.
When it comes to reducing the dangers associated with hydraulic hose failures, Flotec can supply the appropriate product and support to do just that.
Importantly, Flotec rail products are EN 45545-2 fire safe compliant.
Flotec’s LifeGuard solution is widely regarded as an industry best-practice and safety critical application.
Flotec can provide official Gates Safe Hydraulics training. Contact the team to find out more.
To find out more about the LifeGuard sleeve and Flotec’s entire industrial product range, call the team on 01509 230 100 or email sales@floteconline.com
Alternatively, head to www.flotecindustrial.co.uk/contact-us and submit an online enquiry.
To find out more and get involved with Rail Safety Week, please visit: www.railsafetyweek.org
You can discover more about the Rail Forum by visiting: https://www.railforum.uk
To view the explainer podcast, visit: https://youtu.be/kqlvuVncBLQ
Get active on social media by using hashtag #RSW23
And of course, rail safety is more than a one-week initiative. Safety on our rail network should be at the forefront of everybody’s mind 24/7/365.

Comments